Case Study: Transforming Logistics Operations with AI Solutions at Synkcode
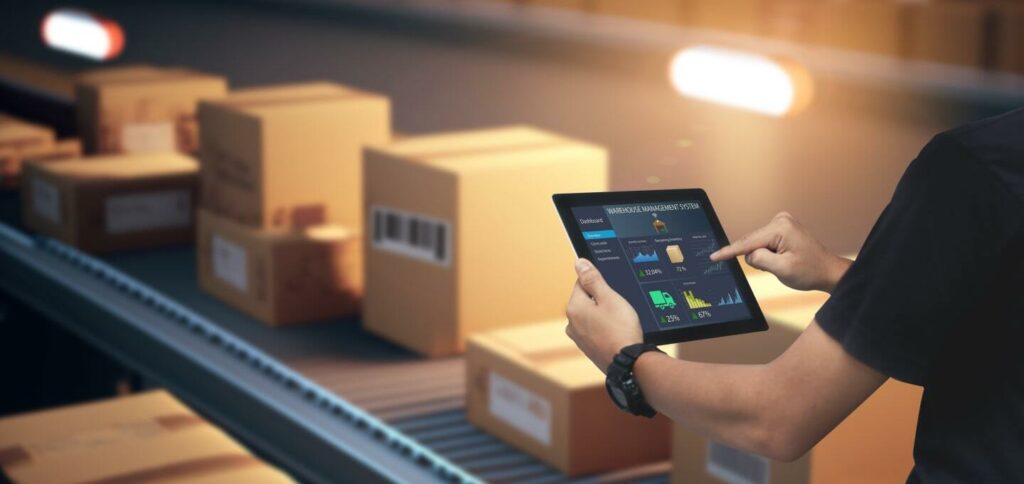
Client Overview
A global logistics provider, managing the movement of goods across multiple regions, was facing increasing challenges related to operational efficiency, route optimization, demand forecasting, and customer satisfaction. Their traditional systems for logistics management relied heavily on manual processes, leading to inefficiencies, higher costs, and delays in deliveries. With the complexity of managing multiple routes, varying demand patterns, and ensuring optimal delivery schedules, the company sought to modernize its operations. The client partnered with Synkcode to implement advanced AI-driven solutions that could streamline their logistics operations, reduce operational costs, and improve customer satisfaction by optimizing delivery routes and forecasting demand more accurately.
The Challenge
The company required a solution that could provide real-time visibility, optimize logistics operations, and ensure that customer needs were met efficiently and cost-effectively. The client’s logistics operation had several critical inefficiencies, including:
Inefficient Route Planning: Existing systems could not dynamically adjust delivery routes based on real-time data, leading to suboptimal routes, longer delivery times, and increased fuel consumption. Drivers often experienced delays due to unforeseen traffic, road closures, or accidents.
Inaccurate Demand Forecasting: The company relied on historical data and manual analysis for demand forecasting, which often resulted in incorrect predictions, leading to either excess inventory or stock shortages.
High Operational Costs: Inefficient route management and poor demand forecasting increased fuel costs, labor expenses, and vehicle wear and tear. The manual processes also required significant administrative resources.
Limited Visibility and Data Utilization: Despite having access to large volumes of data across their operations, the company lacked an intelligent system that could analyze this data in real time to provide actionable insights and proactive decision-making.
Customer Satisfaction Issues: Due to inconsistent delivery schedules and delays, customer satisfaction levels were declining, leading to increased complaints and a loss of business to competitors offering faster and more reliable delivery services.
Synkcode’s Solution: AI-Driven Logistics Optimization
Synkcode implemented a comprehensive AI-powered logistics solution tailored to address the client’s unique challenges. The solution leveraged Artificial Intelligence (AI), Machine Learning (ML), and predictive analytics to transform logistics operations, automate decision-making, and enhance overall efficiency.
Here’s how Synkcode’s AI solution addressed the client’s challenges
AI-Powered Route Optimization
Synkcode deployed an AI-based route optimization engine that dynamically calculated the most efficient routes for delivery vehicles, taking into account real-time traffic data, road conditions, weather, and delivery priorities.
How It Works: The AI solution collected and analyzed real-time data from GPS devices, traffic monitoring systems, and historical delivery patterns. By processing this data, the system recommended the best possible routes, reducing delays and fuel consumption. The AI continuously updated routes in response to changes in traffic conditions or new delivery requests.
Impact: Route optimization reduced fuel consumption by 20%, shortened delivery times by 15%, and minimized the number of miles driven. This not only cut costs but also improved on-time delivery rates, boosting customer satisfaction.
Predictive Demand Forecasting
Synkcode’s AI solution integrated predictive analytics to improve demand forecasting accuracy. The AI model utilized historical data, current market trends, weather patterns, and regional events to predict future demand for products more effectively.
How It Works: Machine learning algorithms continuously analyzed past sales data, seasonal trends, and other external factors that could impact demand. The AI forecasted demand with a higher level of accuracy than manual processes, allowing the company to prepare inventory and resources accordingly.
Impact: Accurate demand forecasting reduced instances of overstocking and stock shortages by 25%, leading to better inventory management and fewer missed sales opportunities. This also enabled more efficient resource allocation, such as assigning vehicles and drivers based on predicted demand.
Real-Time Monitoring and Predictive Maintenance
Synkcode’s AI solution provided real-time monitoring of the company’s fleet, collecting data on vehicle performance, fuel efficiency, and maintenance needs. The system also used predictive maintenance algorithms to forecast when vehicles were likely to require service or repairs, preventing breakdowns and reducing downtime.
How It Works: AI sensors installed in vehicles transmitted data to a central dashboard, where the AI analyzed key metrics such as engine performance, fuel consumption, and wear and tear. The system predicted maintenance needs based on usage patterns, vehicle condition, and historical data.
Impact: Predictive maintenance reduced vehicle downtime by 30%, extended the lifespan of the fleet, and reduced repair costs by 18%. This contributed to the overall efficiency of the logistics operation by ensuring that vehicles were always in optimal working condition.
Automation of Logistics Processes
To further streamline operations, Synkcode implemented AI-driven automation for repetitive tasks, such as shipment scheduling, customer notifications, and inventory restocking.
How It Works: AI bots automatically handled administrative tasks like assigning drivers, updating delivery schedules, sending real-time notifications to customers, and triggering inventory replenishment based on demand predictions. This reduced the need for manual intervention and allowed staff to focus on more strategic tasks.
Impact: Automated processes reduced administrative workloads by 40% and improved operational efficiency. Customers were kept informed of delivery times through automated notifications, enhancing the overall delivery experience.
AI-Enhanced Customer Service
Synkcode integrated AI-powered chatbots and support systems to handle customer queries related to deliveries, tracking, and order status. These chatbots were capable of handling a high volume of inquiries, providing instant answers, and escalating complex issues to human agents when necessary.
How It Works: AI-driven chatbots interacted with customers through multiple channels (e.g., website, app, and email), providing them with real-time updates on their deliveries, answering questions, and helping resolve issues without human intervention. The AI also analyzed customer feedback to identify patterns and recommend operational improvements.
Impact: AI-enhanced customer service improved response times, resolved 70% of queries without human intervention, and increased overall customer satisfaction by 25%.
Conclusion
By leveraging AI and machine learning technologies, Synkcode transformed the client’s logistics operations, making them more efficient, cost-effective, and customer-focused. The implementation of AI-powered route optimization, predictive demand forecasting, real-time monitoring, and process automation resulted in significant cost savings, reduced delivery times, and improved customer satisfaction.
Synkcode’s AI solution not only solved the client’s immediate logistical challenges but also positioned the company for continued growth and scalability in a highly competitive industry. This case study highlights Synkcode’s expertise in using AI to deliver innovative solutions that drive operational excellence and business success.